proceso de contacto es un proceso para la producción de ácido sulfúrico por medio de un catalizador (usualmente, pentóxido de vanadio en sílice). El método lo patentó Peregrine Phillips12 en 1831.34 Se ha aplicado a escala industrial, este método ha evolucionado y se emplea la versión doble más rentable y ecológica. Anteriormente también se utilizaba el proceso de cámaras de plomo y el proceso del vitriolo.
Descripción del proceso[editar]
En el primer paso es producir dióxido de azufre por la combustión de azufre con el oxígeno del aire. El aire empleado en la combustión debe ser lo suficientemente seco, para evitar la corrosión y la desactivación del catalizador, con lo que el producto resultante sería ácido sulfuroso.
La combustión de azufre está en exceso de aire en un horno con un revestimiento refractario a un gas con aproximadamente 10 a 11% de contenido de azufre. La temperatura del gas después de la combustión debe bajarse hasta aproximadamente 410 a 440 ° C para la subsiguiente etapa de la oxidación catalítica.
El dióxido de azufre reacciona con oxígeno en presencia de un catalizador, de platino - o vanadio - (en gel de sílice SiO2), en una reacción de equilibrio a trióxido de azufre. La misión del catalizador es aumentar la velocidad de reacción pero no cambia el punto de equilibrio. De acuerdo con el principio de Le Chatelier, una temperatura más baja desplaza el equilibrio químico hacia la derecha, por lo tanto, aumenta el rendimiento porcentual. Si al bajar la temperatura también baja la velocidad de formación pudiendo llegar a un nivel antieconómico. Como compromiso entre los dos condicionantes las altas temperaturas se sitúa entorna a los 450 ° C, las presiones medias entre 1 a 2 atm. Como la reacción es exoterma después de pasar por una bandeja de catalizador el gas se saca del reactor y se enfría hasta los 400ºC antes de volver a introducirlo, para conseguir el proceso lo más isotermo posible.
Aunque se podría hacer reaccionar el trióxido de azufre resultante con agua para formar ácido sulfúrico.
Pero no se hace debido a que es una reacción fuertemente exotérmica y haría hervir la mezcla produciendo vapores o nieblas ácidas. En su lugar se aprovecha que el SO3 tiene una mayor solubilidad en H2SO 4 que en el agua. Esto crea disulphuric (también conocido como ácido sulfúrico fumante o óleum):
Este se puede mezclar con agua para obtener el doble de ácido sulfúrico.
Como norma las plantas de ácido sulfúrico más, que la solución de SO3 sobre 97 a 99% de fuerza se utiliza ácido sulfúrico, y la concentración de ácido sulfúrico por adición de agua se ajusta de modo que no se forme nada de ácido sulfúrico fumante. En algunas plantas de ácido sulfúrico también se hace consciente de óleum, que luego no se diluye con agua, sino que se utiliza para usos específicos.
Es importante que en la reacción de dióxido de azufre con oxígeno para dar trióxido de azufre la temperatura no salga del rango de 400-700 °C. Por debajo de los 400ºC el catalizador no es efectivo y por encima de 700ºC los materiales del reactor sufren demasiado estrés.
Fuentes del SO2[editar]
Para este proceso se puede agrupar en dos formas de obtener el SO2 uno por la quema de azufre nativo y la otra mediante sustancias en el que el azufre aparece con impurezas: la tostación de piritas, la regeneración de ácido sulfúrico gastado, el ácido sulfhídrico. Esto condiciona la pureza del SO2.
La producción de ácido sulfúrico por combustión de azufre elemental presenta un mejor balance energético pues no tiene que ajustarse a los sistemas de depuración tan rígidos forzosamente necesarios en las plantas de tostación de piritas. Primero de debe secar el aire de combustión, es decir quitarle la humedad para lo cual se pasa por una torre de secado. Esta consiste en una ducha de ácido sulfúrico donde se aprovecha la gran avidez de este por el agua. Al salir del horno después de la combustión se pasa por una caldera con el fin de bajar su temperatura, el calor retirado se emplea para fundir el azufre que se va a quemar. A continuación se pasa por un filtro para retirar las cenizas y posibles sólidos.
EL caso mas extremo se trata del tostado de piritas, una fuente con muchas impurezas, el proceso de purificación es más complejo lo que influyen sensiblemente sobre el rendimiento general de la planta. El aire para la combustión se seca de la misma forma, pero después de la combustión se separan las cenizas mediante un filtro. El polvo producido en el proceso de tostación nunca puede eliminarse en su totalidad y, junto con las impurezas, principalmente arsénico y antimonio. Estos pueden envenenar al catalizador lo que haría disminuir el rendimiento. Después pasa por una torre de lavado que mediante una ducha de ácido sulfúrico débil al 5% se limpia y enfría el gas. Después pasa a una torre de secado mediante una ducha de ácido sulfúrico concentrado. Existen diversos filtros para eliminar sustancias perjudiciales como el arsénico. Antes de introducir el gas en el reactor catalítico se ajusta la temperatura.
Cuando se parte de ácido sulfúrico gastado o ácido sulfhídrico se debe mantener la temperatura de la llama elevada para asegurar la total conversión en SO2 lo cual puede implicar el empleo de algún combustible.
Catálisis[editar]
La etapa de reacción esencial es la oxidación de dióxido de azufre con aire oxígeno a trióxido de azufre con la ayuda un catalizador. El mejor es el platino pero tiene dos inconvenientes que hace que no se emplee, el primero, es muy susceptible a la impurezas especialmente de arsénico y se envenena rápidamente y el segundo, es muy caro. Por eso el catalizador empleado normalmente es el pentóxido de vanadio. La empresa BASFpatentó el empleo de pentóxido de vanadio en 19135 Los reactores suelen tener cuatro bandejas de reacción. Como la reacción es exotérmica a la salida de cada bandeja el gas se envía a un intercambiador de calor para disminuir la temperatura y entre en la siguiente bandeja a la temperatura óptima.
El pentóxido de vanadio se encuentra en los poros de la tierra de diatomeas incluye como un sólido, pero se disuelve en el estado activo en una masa fundida de sulfato de metal alcalino. La temperatura de fusión del sulfato de metal alcalino, por lo tanto, es límite inferior de funcionamiento del catalizador. Se estudia el empleo de catalizador de cesio que tiene una temperatura límite inferior más abajo, lo que permite disminuir la temperatura final de los gases y no hacer sufrir al acero tanto estrés.67
Se puede considerar que el proceso de catálisis ocurre en dos etapas dos etapas con un total de dos moléculas de dióxido de azufre para reaccionar con el oxígeno a trióxido de azufre. El mecanismo de la acción del catalizador comprende dos pasos:
1. La oxidación del SO2 en SO3 por V5+ :
2. La oxidación de V 4 + nuevo en V 5 + por el oxígeno (regeneración del catalizador):
Pero el proceso real es algo más complejo pasando por un complejo de composición [(VO)2O(SO4)4]4-. En este el oxígeno se deposita primero, seguido por el dióxido de azufre.
A veces también se emplea óxido de hierro como catalizador pero se obtiene peores resultados.
Variación de doble contacto[editar]
El proceso de doble contacto para la producción de ácido sulfúrico es una evolución del proceso de contacto, pero mejorado en la parte medio ambiental y por tanto se utiliza ahora industrialmente.
En contraste con el método de contacto simple, el gas, mezcla de SO2 y SO3, después de paso a través de tres bandejas de catálisis va a una torre de absorción intermedia donde con ácido sulfúrico al 98% se absorbe la mayoría del SO3. El pequeño porcentaje no absorbido junto con el SO2 pasan por una cuarta bandeja. Donde se convierte la mayor parte del SO2 en SO3 ya que el equilibrio se ve favorecido según el principio de Le Chatelier. Y a continuación pasa por otra torre de absorción. El rendimiento obtenido es por lo menos 99,8%. Un pequeño porcentaje de SO2 y trazas de SO3 se lanza a la atmósfera.
Como la temperatura en la torre de absorción debe ser relativamente baja, pero el gas de retorno al reactor debe estar a unos 400ºC existe una serie de intercambiadores de calor intermedios con el fin de ajustar las temperaturas y aprovechar el calor.
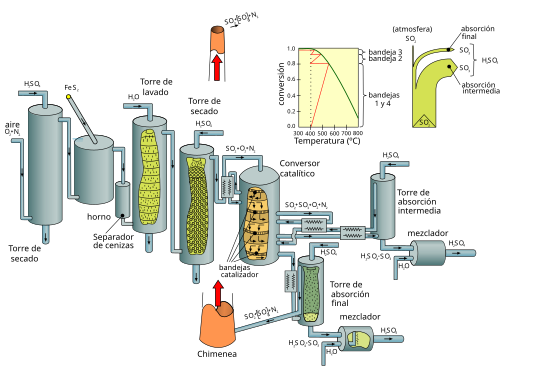
proceso de Ostwald es un proceso químico para producir ácido nítrico, que fue desarrollado por Wilhelm Ostwald y patentado en 1902. Es uno de los principales pilares de la industria química moderna.
Se asocia históricamente y en la práctica al proceso de Haber que proporciona la materia prima indispensable, el amoníaco.
Descripción[editar]
El amoníaco se convierte en ácido nítrico en dos etapas. Es oxidado calentando con oxígeno en presencia de un catalizador tal como el platino con un 10% de rodio para formar óxido nítrico y agua. Este paso es fuertemente exotérmico, siendo una fuente de calor muy útil una vez iniciada (ΔH = -950 kJ/mol):
- 4 NH3 (g) + 5 O2 (g) → 4 NO(g) + 6 H2O (g)
El segundo paso se realiza en presencia de agua en una torre de absorción. El óxido nítrico se oxida otra vez para producir dióxido de nitrógeno (NO2):
- 2 NO (g) + O2 (g) → 2 NO2 (g)
Este gas es absorbido fácilmente por el agua, rindiendo el producto deseado (ácido nítrico, no obstante en una forma diluida), mientras que reduce una porción de ella de nuevo a óxido nítrico:
- 3 NO2 (g) + H2O (l) → 2 HNO3 (l) + NO (g)
El NO se recicla y el ácido se concentra por destilación. Esto es alternativo si el paso anterior se realiza en el aire:
- 4 NO2 (g) + O2 (g) + 2 H2O (l) → 4 HNO3 (aq)
Las condiciones típicas para la primera etapa, que contribuyen a una producción total de cerca de 96%, son: presión entre 4 y 10 atmósferas (400-1010 KPa o 60-145 psig) y temperatura de 1173 K (aproximadamente 900 °C o 1652 °F).
Reacciones secundarias[editar]
Hay que tener en cuenta una complicación debido a una reacción secundaria en la primera etapa que disminuye el rendimiento:
- 4 NH3 + 6 NO → 5 N2 + 6 H2O
- Esta reacción es minimizada reduciendo el tiempo que la mezcla de gases están en contacto con el catalizador.
Historia[editar]
Una patente anterior (Kuhlmann, 1838) describió la química básica, pero el amoníaco (de fuentes animales) era escaso entonces y su interés era puramente académico cuando Ostwald patentó su versión en 1902. De haberse conocido entonces el método de síntesis de amoníaco (patentado por Fritz Haber en 1908) habría cambiado la perspectiva enteramente. Las contribuciones primarias de Ostwald parecen haber sido las referentes a las condiciones del catalizador y de funcionamiento, una cuestión quizás más de ingeniería química que de ciencia básica.
Antes de esto la fuente de la mayoría del nitrógeno industrial era minerales de nitrato, sobre todo el nitrato de Chile, del cual se obtenía ácido nítrico por tratamiento con ácido sulfúrico. El proceso de Ostwald ganó prominencia como complementario al proceso de Haber) en la fijación del nitrógeno atmosférico. Ambos procesos combinados prolongaron indudablemente la Primera Guerra Mundial, cuando las fuentes en altamar de Alemania fueron cortadas y la producción de explosivos amenazada. El uso de materias primas extensamente disponibles y de bajo coste condujo posteriormente a su adopción general, dando por resultado un consumo creciente del nitrógeno, sobre todo como fertilizante.
El proceso se realizaba inicialmente en recipientes de gres a presión baja, pero la introducción del acero inoxidable hizo posible presiones más elevadas y por tanto producciones más altas.
El proceso de Verneuil, también denominado de fusión por llama, fue el primer método comercial de fabricación sintética de piedras preciosas, desarrollado en 1902 por el químico francés Auguste Verneuil (1856-1913). Se utiliza principalmente para producir rubís y zafiros, variedades de corindón, así como las imitaciones de diamantes: rutilo y titanato de estroncio.
El principio del proceso consiste en fundir una sustancia finamente pulverizada con una llama de oxihidrógeno, cristalizando las gotas fundidas en una bola. El proceso se considera el inicio de la moderna industria tecnológica del crecimiento de cristales, y sigue siendo ampliamente usado en la actualidad.
Historia[editar]
Desde la época de los alquimistas, ha habido intentos para producir sintéticamente las piedras preciosas. El rubí, siendo una de las cinco apreciadas gemas cardinales, ha sido un candidato ideal para la síntesis. En el siglo XIX, esos intentos tuvieron éxito, con el rubí primero producido por la fusión de dos rubíes más pequeños en 1817, y los primeros cristales microscópicos creados a partir de alúmina (óxido de aluminio) en un laboratorio en 1837. En 1877, el químico Edmond Frémyhabía ideado un método eficaz para la fabricación de rubíes comerciales mediante el uso de baños de metal fundido en alúmina, produciendo piedras con calidad de gema. El químico parisino Auguste Verneuil colaboró con Fremy en el desarrollo del método, pero pronto pasó a desarrollar de forma independiente el proceso de fusión por llama, que con el tiempo llevaría su nombre.
Una de las fuentes de inspiración de Verneuil para desarrollar su propio método fue la aparición de rubíes sintéticos vendidos por un comerciante desconocido de Ginebra en 1880. Estos "rubíes de Ginebra" no se consideraron artificiales en su momento, pero ahora se cree que son los primero rubíes producido por fusión de llama, 20 años anteriores a la labor de Verneuil. Después de examinar los "rubíes de Ginebra", Verneuil llegó a la conclusión de que era posible recristalizar óxido de aluminio finamente molido en una piedra de gran tamaño. Esta toma de conciencia, junto con la disponibilidad de la antorcha detonante desarrollada recientemente y la creciente demanda de rubíes sintéticos, le llevó a diseñar el horno de Verneuil, donde finalmente consiguió fundir alúmina purificada y óxido de cromo en una llama de por lo menos 2000 °C, y se recristalizaron en un soporte bajo la llama, creando un gran cristal. Anunció su trabajo en 1902, y publicó los detalles describiendo el proceso en 1904.
En 1910, el laboratorio de Verneuil había crecido hasta convertirse en una planta de producción con 30 hornos. La producción anual de la piedra preciosa por el proceso Verneuil era de unos 1.000 kg en 1907. En 1912, la producción llegó a 3.200 kg, y llegaría a alcanzar las 200.000 kg en 1980 y 250.000 kg en el año 2000, siendo dirigida la fábrica de Monthey, Suiza, fundada en el año 1914, por Hrand Djevahirdjian. Las mejoras más notables en el proceso se realizarón en 1932, por S.K. Popov, quien contribuyó a desarrollar la capacidad de producción de zafiros de alta calidad en la Unión Soviética a lo largo de los 20 años siguientes. Una gran capacidad de producción se desarrolló también en los Estados Unidos durante la Segunda Guerra Mundial, cuando las fuentes europeas fueron cortadas, y había una gran demanda de estas gemas por sus aplicaciones militares.
El proceso fue diseñado inicialmente para la síntesis de rubíes, que se convirtieron en las primeras piedras preciosas que se produjeron sintéticamente, gracias a los esfuerzos de Fremy y Verneuil. Sin embargo, el proceso Verneuil también puede utilizarse para la producción de otras piedras, como el zafiro, que simplemente requiere sustituir el óxido férrico por óxido de cromo. Para otras gemas más elaboradas, como los zafiros estrella, se agrega titanita (dióxido de titanio) y la bola se mantiene caliente durante más tiempo, permitiendo cristalizar las agujas de rutilo en su interior. Desde 1947 la Linde Air Products Division de Union Carbide había sido pionera en el uso del proceso de Verneuil para la creación de zafiros estrella, hasta que la producción se interrumpió en 1974 por la competencia en el extranjero.
A pesar de algunas mejoras en el método, el proceso Verneuil se mantiene prácticamente inalterado hasta nuestros días, manteniendo una posición de liderazgo en la fabricación de corindón sintético y espinela. Su revés más importante llegó en 1917, cuando Jan Czochralski presentó el proceso Czochralski, que ha encontrado numerosas aplicaciones en la industria de los semiconductores, donde se requiere un aumento de la calidad de los cristales que el proceso Verneuil en parte no puede producir. Otras alternativas para el proceso surgieron en 1957, cuando los Laboratorios Bell presentaron el proceso hidrotérmico, y en 1958, cuando Carroll Chatham presentó el proceso de flujo. En 1989 Larry P. Kelley de TIC, Inc. también desarrolló una variante del proceso Czochralski donde se utiliza un rubí natural como "semilla" del nuevo material producido.
El proceso[editar]
Uno de los factores más cruciales en el éxito de cristalizar una piedra artificial es la obtención de materia prima altamente pura, con al menos el 99,9995% de pureza. En el caso de la fabricación de rubíes o zafiros, este material es la alúmina. La presencia de impurezas de sodio es especialmente negativa, puesto que hace que el cristal sea opaco. Dependiendo de la coloración deseada del cristal, se añaden pequeñas cantidades de diversos óxidos, como el óxido de cromo para un rubí rojo, o el óxido férrico y dióxido de titanio para un zafiro azul. Otras materias primas incluyen dióxido de titanio para la producción de rutilo, o doble titanilo oxalato para la producción de titanato de estroncio. Por otra parte, se pueden utilizar como materia prima pequeños cristales naturales del producto deseado carentes de valor.
La materia prima esta en forma de polvo fino y se coloca en un contenedor dentro del horno de Verneuil, con una abertura en la parte inferior a través de la que el polvo puede escapar cuando el contenedor se hace vibrar. A la vez que el polvo sale, se suministra oxígeno al horno, y viaja junto con el polvo por un tubo estrecho. Este tubo está situado dentro de un tubo más grande, en el cual se suministra hidrógeno. En el punto donde el tubo estrecho se abre en el más grande, se produce la combustión, con una llama de por lo menos 2000 °C en su núcleo. El polvo pasa a través de la llama, y se derrite en gotitas pequeñas, que caen en una varilla de soporte situada a continuación. Las gotas poco a poco forman un aglomerado en forma de cono en la barra, cuya punta debe mantenerse suficientemente cerca del núcleo de la llama para que se mantenga líquida. Es en ese extremo semilla donde el cristal se forma con el tiempo. A medida que caen más gotas en la punta del cristal, comienza a formarse "la bola" y el apoyo se mueve lentamente hacia abajo, permitiendo que la base de la bola se cristalice, mientras que su límite superior permanece siempre en estado líquido. La bola crece con la forma de un cilindro cónico, con un diámetro que se va ampliando en función de la distancia a la base, y finalmente se mantiene más o menos constante. Con un suministro constante de polvo y la retirada progresiva del soporte, se pueden obtener bolas muy largas. El cristal se deja enfriar una vez retirado del horno, y la bola se divide a lo largo de su eje vertical para aliviar las tensiones internas, porque de lo contrario el cristal será propenso a la fractura durante el tallado.
Cuando describió inicialmente el proceso, Verneuil especificó una serie de condiciones fundamentales para obtener buenos resultados. Estos son: una temperatura de llama que no sea mayor de lo necesario para la fusión; mantener siempre el producto fundido en la misma zona de la llama detonante; y la reducción del punto de contacto entre el producto fundido y el apoyo a un área tan pequeña como sea posible. El promedio de producción comercial usando el proceso es de 13 mm (0,5 pulgadas) de diámetro y de 25 a 50 mm (1 a 2 pulgadas) de largo, pesando alrededor de 125 quilates (25 g). El proceso también puede realizarse con la orientación predeterminada de un cristal semilla para lograr una orientación cristalográfica específica.
Los cristales producidos por el proceso Verneuil son química y físicamente equivalentes a sus homólogos naturales y generalmente es muy difícil distinguir unos de otros. Una de las características indicadoras de un cristal artificial fabricado por el método Verneuil son las líneas curvas de crecimiento (estrías curvas) formadadas cuando la bola cilíndrica crece hacia arriba en un entorno con un alto gradiente térmico; las líneas equivalentes en los cristales naturales son paralelas. Otra característica distintiva es la presencia común de burbujas de gas microscópicas formadas debido al exceso de oxígeno en el horno; las imperfecciones de los cristales naturales son, por lo general, impurezas sólidas.
No hay comentarios:
Publicar un comentario